The expansion which mankind has witnessed in terms of scientific revolution, population and growth in the 21st century is unprecedented in history.
Industrialization has no doubt brought comfort in our daily lives but at the expense of our natural resources, which are of course limited.
The level of consumption of resources associated with modern development is pushing the international community of researchers to explore more sustainable solutions for our built environment.
The cement industry owing to the rapid urbanization is the backbone of our modern built environment and one of the largest consumers of natural resources.
Cement-based materials currently represent more than one-third of the natural resources extracted from earth annually. The consumption is likely to increase in the coming decades following the patterns of growth suggested by economic agencies. This situation signifies the importance of identifying resource-efficient pathways for the cement industry.
In addition to that, the carbon emissions associated with cement manufacturing are alarming. In a business-as-usual scenario, the cementitious materials would be responsible for 30% of the world’s CO2 emissions by 2050.
Currently, cement industry accounts for approximately 7% of the total anthropogenic CO2 emissions worldwide, making cement the second largest CO2contributor in industry after power plants with an associated production volume of more than 4 billion tons annually.
As of today, the operational capacity of cement production in Pakistan is estimated to be 46- 49 million tons, with an expected expansion to 76 million tons by 2020.
The cement industry contributes billions to Pakistan’s economy. In 2016, it provided approximately Rs. 20 billion to the national exchequer alone, over Rs. 40 billion is added to the country’s GDP annually.
In 2015, the cement industry contributed up to 13% of total CO2 emissions in Pakistan. The country is the world’s 14th largest cement producer and any efforts employed towards improvisation will not only benefit the economy but also the environment at large which is in imminent threat due to increasing carbon emissions.
The most effective strategy to reduce CO2 emissions and consumption of natural resources by cement production lies in reducing its clinker content. This can be achieved by substitution of clinker with reactive materials, which up to now have typically been industrial byproducts: fly ash from coal-fired power stations and blast furnace slag. However, supplies of these materials are limited compared to the amount of cement produced worldwide. The major innovation is to combine the use of abundantly available low-grade kaolinite clay with a further 15% of limestone, with no reduction in mechanical performance. This will not only reduce the cost of cement per ton but also the carbon emission by 30%
We, at NED University of Engineering and Technology, are currently working on the feasibility study of eco-friendly cement based on Limestone and Calcined Clays. The research is aimed at finding out the potential of alternative cementitious materials, specifically Limestone-Calcined-Clay-Cement, also known as LC3, in Pakistan. Preliminary data of available raw materials suggest a promising future for the commercial viability of LC3 cement blend in Pakistan.
We hope that through our efforts and with the support of industrial and research sector of Pakistan, this project will contribute towards a carbon-free and a sustainable future providing low-cost alternatives to cement industry of Pakistan.
(The author is an Undergraduate student of Mechanical Engineering Department, NED University of Engineering and Technology working on a research project with his fellow students.) n
Exploring Sustainable Solutions for Cement Industry of Pakistan
on 21/03/2019
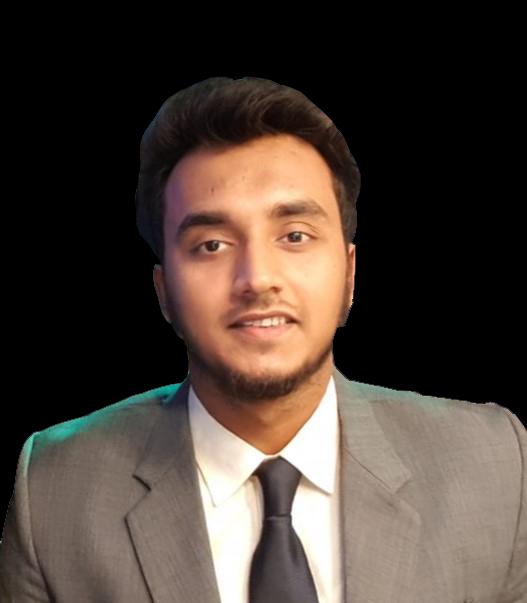